Tailings and waste
Sustainable waste management
GRI 306-1, 306-2, SASB EM-MM-150a.10, EM-MM-540a.2In accordance with the Russian laws, the Company maintains records of waste generated, treated, recovered, neutralised, transferred to or received from third parties, and disposed of; these records are aggregated on a quarterly and annual basis. The Company aims to monitor waste management throughout its entire life cycle, including the management of waste by third parties. Contracts for further waste management are made with third parties possessing all necessary permits, licences, state expert conclusions, technical regulations and specifications.
More than 99% of waste generated by the Company is associated with mining and concentration and is not hazardous as this is overburden and host rock (hazard class 5), and tailings (hazard classes 4 and 5)Hereinafter hazard classes are as per the waste hazard classification adopted in Russia..
All other waste not associated with mining and concentration is a result of various production or other economic activities, or comes from materials and products that have lost their consumer properties after having been used according to their intended purpose.
The most hazardous waste generated by the Company is hazard class 1 (extremely hazardous) and hazard class 2 (highly hazardous) waste. The majority of this waste is mercury lamps and thermometers, batteries, acids and alkalis used in batteries, uninterruptible power supplies, and oils.
Hazard classes 1 and 2 waste is below 0.001% of the total waste generated. In 2022, hazard classes 1 and 2 waste amounted to 57 t.
In compliance with the new legal requirements, in March 2022 Nornickel switched to a new procedure for managing hazard classes 1 and 2 waste, which includes the use of the dedicated state information system. As a result, in 2022:
- the Group companies generating hazard classes 1 and 2 waste entered into contracts with the Russian Environmental Operator for hazard classes 1 and 2 waste management;
- a series of meetings on the management of hazard classes 1 and 2 waste and on the performance of the federal state information system were held jointly with the Russian Environmental Operator;
- the business process target map for using the Federal State Information System for the Accounting and Monitoring of Hazard Class 1 and Hazard Class 2 Waste was developed from the moment of registering with the system to signing the primary accounting documents.
The total amount of waste generated in 2022 increased due to the expansion of production activities (mining and concentration), as well as implementation of a programme on land clean-up and dismantling of unused buildings and structures, which resulted in the generation of construction waste in the Norilsk Industrial District.
Contribution to combating contamination with waste
GRI 306-2, 306-4Nornickel strives to foster non-waste production by developing and implementing waste recovery approaches, making efforts to clean up existing pollution. Waste generated by the Company is used by third parties and Nornickel itself for backfilling of mined-out areas and pits, road filling, building of tailing dumps, and placement in waste dumps. Recovery provides for the economic utilisation of waste and reduction of landfill disposal, which helps minimise adverse environmental impact.
An increase in waste disposal in 2022 was due to the use of overburden in own operations (road backfilling, strengthening of tailing dumps, site levelling).
In 2022, the Company continued implementing the Clean Norilsk Project to clean up industrial and construction waste.
To implement the Project, in 2020 the Company’s Polar Division established dedicated units tasked with:
- dismantling of unused and dilapidated buildings and structures;
- clean-up of production waste and scrap metal;
- removal of waste and scrap metal to special landfills and processing sites;
- clean-up of waste and scrap metal in hard-to-reach locations of the forest-tundra area;
- implementation of land rehabilitation measures;
- processing of collected scrap into charge for further transportation.
Since the start of the Clean Norilsk programme in 2021, 262 dilapidated buildings have been dismantled, 71 kt of scrap metal and 814 kt of waste collected and removed, and an area of 2.6 million m2 cleaned. The technical phase of disturbed land rehabilitation was carried out on an area of 78.8 ha. Total costs since Clean Norilsk was implemented have exceeded RUB 11 bn.
By 2030, Nornickel plans
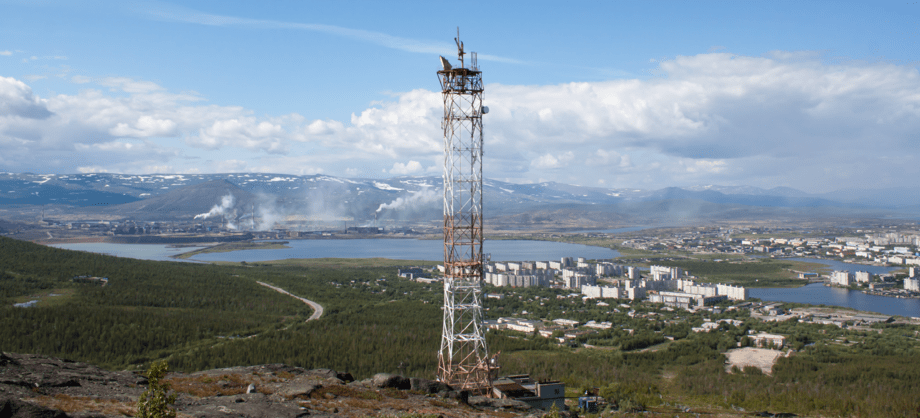
Waste disposal
Tailing dumps
SASB EM-MM-540a.1, EM-MM-540a.2Nornickel takes a responsible approach to tailings management, paying particular attention to their physical and technological safety.
In 2021, the Company put in place a Tailings Management Policy, which is fundamental for managerial decision-making.
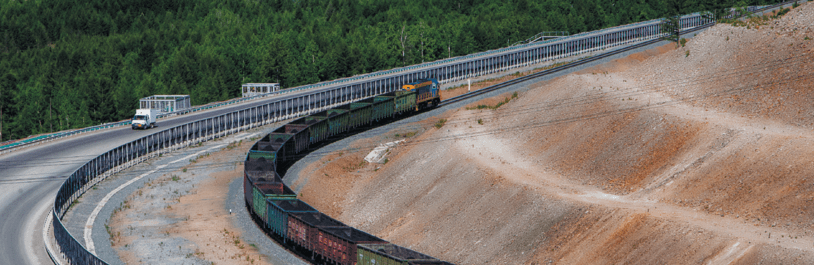
A gypsum storage facility is also under construction in Norilsk.
The Company regularly monitors the condition of hydraulic structures of tailing dumps and conducts environmental monitoring in the adjacent areas.
Nornickel complies with the Russian laws associated with tailings management. Additionally, we developed mandatory safety criteria to operate each tailing dump and had them approved by regulators. The Company regularly reviews the time frames for decommissioning of tailing dumps and determines the future closure and land rehabilitation costs. Based on the results, the Company calculates the present value of future costs, recognising its environmental provision with respect to the tailing dumps.
Nornickel takes a risk-based approach to tailings management. To address tailing dump-related risks, the Company has organisational units and officers providing regular reports to the management. Such units engage qualified and experienced staff. The hydraulic structures are constantly monitored by the operating personnel and a dedicated environmental team.
In addition to the Company’s initiatives, Rostechnadzor carries out annual pre-flood inspections of hydraulic structures together with Nornickel employees. Every five years, the hydraulic structures are subject to detailed inspections by a Rostechnadzor-certified agency that issues an industrial safety declaration upon which Rostechnadzor carries out a comprehensive audit.
SASB EM-MM-540a.3There are two processes in place to assess the Company’s tailing dump-related risks:
- estimates of potential damage to life and health of individuals, and to property of individuals and legal entities as a result of an emergency at a hydraulic structure. Estimates of potential damage serve to identify possible emergency scenarios and assess emergency risks and the negative impact on communities, ecosystems and critical infrastructure;
- assessment of technical and production risks carried out in line with Nornickel’s Regulations on Technical and Production Risk Management.
Potential damage estimates show minimum risks for local communities, ecosystems and critical infrastructure in case of an emergency, as all of the tailing dumps operated by Nornickel are located away from production facilities and residential areas.
Nevertheless, the Company develops emergency preparedness and response plans for worst-case scenarios, as required by the Russian laws. The plans determine roles, responsibilities, and communication procedures.
The emergency preparedness and response plans as well as the public warning system are subject to periodically testing. At least once every five years, when developing a safety declaration Nornickel runs comprehensive drills to verify its preparedness for containing and eliminating emergencies at hydraulic structures. These drills are attended by experts from EMERCOM. If successful, an opinion is issued on the company’s readiness to contain an emergency at a hydraulic structure and protect local residents.
Nornickel has all necessary material and financial resources required to respond to an emergency at its tailing dumps and promptly repair any damage, including a sufficient fleet of excavators, dump trucks and other special vehicles (as outlined in contingency plans). Employees operating the tailing dumps undergo regular dedicated training and knowledge tests mandated by Rostechnadzor.