Occupational health and safety
Human capital GRI 403–1
At Nornickel, we give priority to the life and health of employees over operational performance both when making management decisions and throughout the entire production. Nornickel’s Occupational Health and Safety Policy outlines the Company’s commitment to creating a safe and healthy environment and fostering sustainable employee motivation for safe workplace behaviour.
Main occupational health and safety goals:
01
Zero catastrophic occupational accidents: prevent accidents at the Company’s facilities that may have negative impact on people from across the Company’s regions and the Company’s production results
02
No work-related fatalities: zero tolerance to any work-related fatalities
03
Safe working conditions and mitigation of mining and processing risks
Health and safety management
Occupational health and safety (OHS) at Nornickel covers all the Company’s employees. It is governed by the Russian laws, international regulations and standards, and internal policies and regulations.
Occupational health and safety responsibilities are allocated among Nornickel’s various governing bodies and business units in line with their terms of reference.
In 2022, the second surveillance audit was conducted at Nornickel’s divisions. The audit results confirm that the Company’s existing health and safety management system conforms to ISO 45001:2018 Occupational Health and Safety Management System international standard.
Following the audits, Bureau Veritas Certification, the certification body, described the OHS management system as mature and well-established and found that the corporate systems of Nornickel’s audited companies met the requirements of the standard.
Contractor safety management
GRI 403–1, 403–2, 403–52022 saw the revision of the standard regulating occupational health and safety at all stages of working with contractors. As a result, the Company was able to improve the level of control and occupational safety for contractors operating at Nornickel’s facilities.
In the domestic market, Nornickel procures production and technical supplies under Master Agreements. As part of centralised procurement, a standalone agreement is signed with each contractor stating that the contractor recognises and commits to generally accepted principles in human rights (which include health and safety) and labour relations, as stipulated by international regulations and in particular the UN Global Compact.
In 2022, the Company revised the general terms regarding health and safety that are included in agreements with contractors. The current amendments focus on avoiding fatalities and non-compliance with the cardinal occupational safety rules and encourage contractors to be proactive on health and safety. This approach is better aligned with the Company’s goals.
All works carried out by contractors in highly hazardous conditions are governed by the respective corporate standard. Work permits, operations certificates and work execution plans (process sheets, guidelines, etc.) must contain safety requirements to be met when organising and performing work. The Company checks compliance with these requirements during each shift.
Prior to commencement of work, contractors’ staff receive pre-job and ad hoc health and safety briefing, including security measures set forth in work execution plans.
On the sites of its facilities, the Group holds regular joint inspections of compliance with safety requirements at work, and OHS council (committee) meetings involving contractor representatives. In case of failure to comply with OHS requirements, contractors are fined.
Workplace injuries
SASB EM-MM-320a.1In 2022, we updated the procedure for collecting information on OHS incidents. These efforts helped improve transparency and quality of incident classification. The revised incident reporting procedure resulted in faster response times while the optimised incident classification opened up more opportunities for further data analysis. Root cause detection and investigation also had a major overhaul, which contributed to more effective incident prevention.
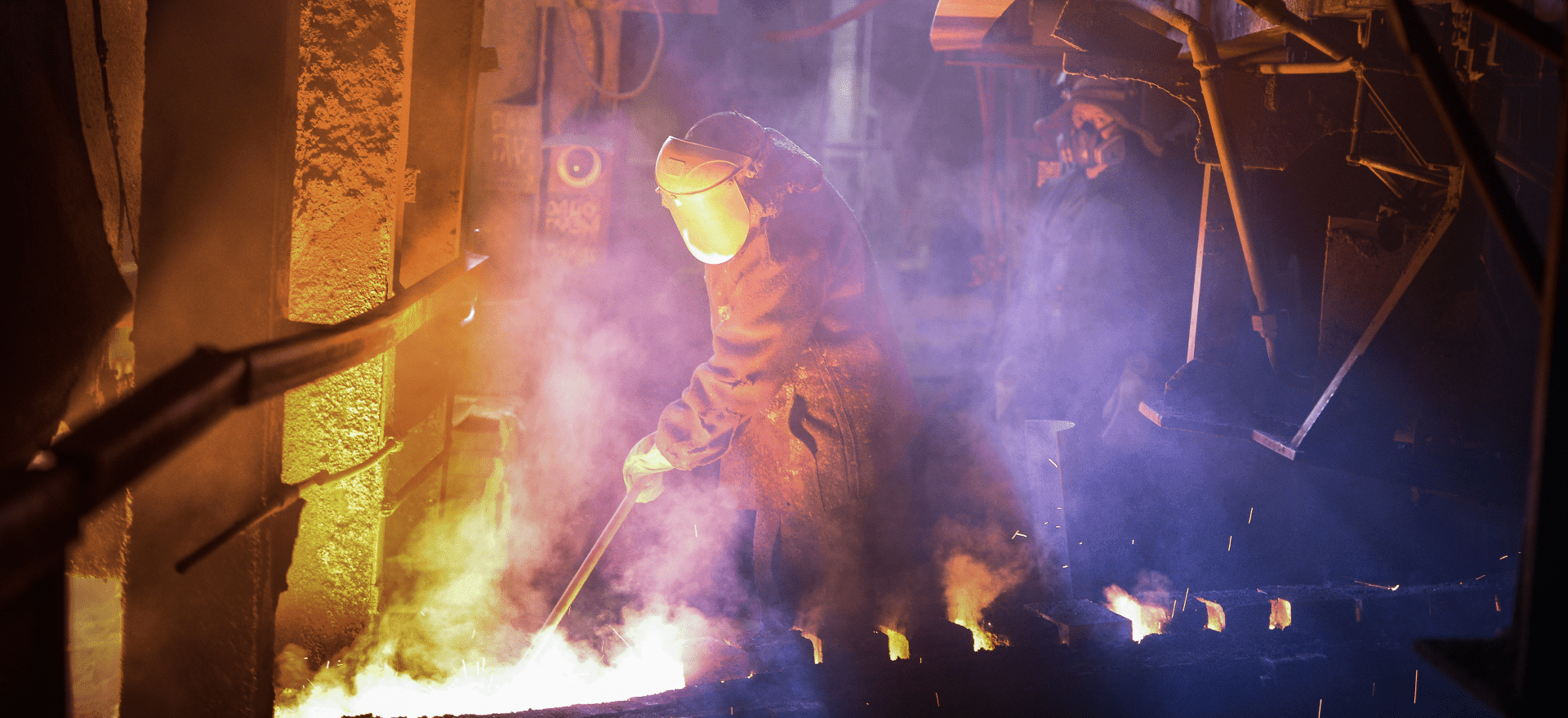
Key workplace injury indicators
GRI 403–9, 403–10
In 2022, the Group had 66 lost time injuries, with lost time injury frequency rate (LTIFR) standing at 0.57. The most frequent reason for injuries was falling from heights. Nornickel’s indicators in this area are in line with the average for the global mining industry.
In 2022, we recorded the lowest number of work-related fatalities. The Group reported four fatalities – this is seven cases fewer than in 2021. Two deaths were caused by rock falling in Kola and Norilsk Divisions, one man died as a result of falling from height, and one drift miner died in a mine accident when driving an electric locomotive.
All circumstances of the fatal accidents were thoroughly investigated and reported on to the Board of Directors.
Based on the results of investigations into the accidents involving rock falling in Kola and Norilsk Divisions, the Company developed and implemented technical measures to mechanise underground workings development, purchased a drilling rig for tunnelling (air core drilling) and mechanical posts for temporary supports and took a number of organisational measures to fulfil the requirements of mine surveyors.
To address the causes of falling from heights on work sites, a panel of workers was tasked to carry out an inspection to check the technical condition of overhead cranes, emergency evacuation routes and the available safety equipment. In 2022, the Company commenced the upgrade of overhead cranes to enable safe emergency evacuation of crane operators. These efforts will continue into 2023.
Following the investigation into the accident with a drift miner who was driving an electric locomotive in Kaula-Kotselvaara mine (part of Severny Mine), Nornickel arranged transportation of workers to workplaces, introduced control over unauthorised driving of electric locomotives and revised the mine railway infrastructure programme.
Nornickel expresses its deepest condolences to the families and friends of the victims and reiterates its commitment to making zero workplace fatalities a key strategic priority. The Company will continue with implementing its programmes to prevent workplace accidents.
OHS system development and mitigation of key risks
GRI 403–1, 403–2
As part of our strategic goal to reduce the occupational injury rate, the Company seeks to continuously improve the elements of its occupational health and safety framework. The changes cover all Operating Unit businesses and all production stages – from mining ore to making metals.
In 2022, we revised our cardinal safety rules, OHS incentive programme and employee awareness raising initiatives. From 2023, employees will be paid incentive compensation for identifying risks at their workplaces.
In the reporting year, Norilsk Concentrator (owned by Medvezhy Ruchey LLC) launched a safety culture transformation project underpinned by a risk-based approach. As part of the project, it carried out:
- an audit of its safety culture and relevant processes;
- a strategic session to define key systematic measures;
- training at pilot workshops;
- work to improve its risk identification and assessment system.
The project helped identify 462 risks, out of which 101 were addressed, with 222 risks identified and reported by mining workers. The project will continue into 2023.
Anyone who identifies a life- and health-threatening risk must report it to the relevant senior manager to address it. If it is impossible to minimise the risk and continue to work safely, the exposed worker has the right to refuse to work if their health and safety is at risk. The procedure for refusing to work is established by the standard “OHS Management System. Hazard Identification, Assessment and Management of Occupational Health and Safety Risks at PJSC MMC Norilsk Nickel”. An employee who refuses to work is required to fill in a checklist and hand it over to their direct supervisor or, if the latter is temporarily unavailable, the relevant senior manager. To confirm acceptance, the supervisor or manager (as the case may be) must fill in, sign and return the tear-off part of the checklist to the worker and give him/her a new checklist. The refusal to work under life- and health-threatening conditions may not constitute grounds for imposing any sanctions on the worker.
In 2022, we continued our work to improve the Control, Management and Security Automated System (CMS AS) and integrate it into broader IT architecture:
- more than five new algorithms implemented to enable notification of responsible persons via corporate email;
- integration between related systems (SAP ERP, SAP BW) and NIKA chatbot completed;
- The unified indicator framework for the corporate sustainability reporting, which is part of the Corporate Data Storage (CDS), successfully embedded to enable online annual report generation using the unified indicator framework for the corporate sustainability reporting with respect to the Group’s injuries data.
In 2022, health and safety expenses increased by 70% y-o-y to RUB 21.6 bn. The increase is due to the development and implementation of additional measures to improve labour conditions, growing headcount and higher costs of personal protective equipment (PPE).
Provision of Personal Protective Equipment
GRI 403–3
Due to the nature of its business, building an efficient operational health and safety system at Nornickel comes with the need to implement a range of organisational safety measures along with providing PPE to its employees exposed to hazardous and harmful workplace factors. Workplaces exposed to hazardous and harmful factors include underground work, operation and maintenance of mining equipment and heavy self-propelled vehicles, extreme climate, etc.
Special assessment of working conditions
In 2022, a special assessment of working conditions covered more than 10,000 workplaces and over 15,000 employees, which amounted to approximately RUB 20.5 mln in expenses for the Group’s operations.
A special assessment of working conditions helps identify hazardous production factors. Whenever these are identified, the Company furnishes employees with free personal protective equipment (PPE), including respiratory protection (respirators, gas masks), hearing protection (earmuffs, earplugs), eye protection (glasses/goggles with UV filters, visors), skin protection (gloves, protective and regenerative creams, protective outerwear).
OHS control and prevention
To avoid workplace injuries, Nornickel regularly implements control and prevention activities.
Health and safety competitions
In 2022, as has become custom at Nornickel, we held individual and team OHS competitions. Team competitions were held across seven groups of Nornickel’s production facilities.
Results of individual competitions were announced with the following awards granted:
- Best Health and Safety Head;
- Best Health and Safety Line Manager;
- Best Health and Safety Specialist;
- Best Health and Safety Compliant Worker.
The Company also runs an ongoing Safe Work communication programme.
Engagement of employees in safety management
GRI 2–26, 403–4
To increase the efficiency of our efforts and promote safety culture, we encourage our employees to get involved in operational health and safety management. Most of the Group companies have in place joint health and safety committees (councils) made up of the management, employees and trade union representatives. The Group companies that have joint committees with trade union bodies employ over 77,000 people (around 97% of the Group’s average headcount).
The Head Office does not have a joint committee as there is no trade union in place, but representatives of the Norilsk trade union take part in HSE Committee meetings. Norilsk Nickel Corporate University (an educational institution not involved in production) does not have committees. Contractors are invited to joint committee meetings that deal with matters related to contractor employees.
Authorised representatives of trade unions and staff in occupational health and safety were elected to participate in preventive activities across the Group’s production units. In the reporting year, 712 representatives of trade unions and staff in occupational health and safety participated in preventive activities. In 2022, they took part in over 11,500 audits and submitted almost 2,600 health and safety improvement proposals.
Health and safety topics covered in formal agreements with trade unions
SASB EM-MM-310a.1
A majority of production companies of the Group have collective bargaining agreements signed with employee representatives (including trade union organisations). The agreements contain occupational health and safety provisions
OHS training
GRI 403–5, SASB EM-MM-320a.1
To improve occupational safety, we implement OHS upskilling initiatives. These include regular briefings on and training courses in occupational health for its employees. We introduced dedicated software modules for specific mining jobs in order to provide health and safety briefings.
In 2022, Nornickel launched a project to create a workplace safety culture coaching system. The project is rolled out at 18 companies employing 42 safety culture coaches. There are two training programmes currently on offer: Dynamic Risk Assessment for mining workers and Behaviour-Based Safety Audit for line managers. The coaches deliver in-person interactive workshops, which are followed by on-the-job training within the real work environment such as a mine or shop. In 2022, more than 5,000 employees completed the Dynamic Risk Assessment programme, which was held 717 times, and 238 employees completed the Behaviour-Based Safety Audit programme, which was held 33 times.
Prevention of occupational diseases
GRI 403–3Heath of its employees is a priority at Nornickel. The Company implements regular measures to prevent occupational diseases.
Regular health monitoring of personnel is key to preventing occupational diseases. Employees undergo compulsory pre-employment, regular and ad hoc medical examinations and check-ups. Those who are involved in hazardous production are subject to additional examinations held at least once in five years by occupational pathology centres or other organisations authorised to conduct pre-employment and regular check-ups. These serve to assess occupational health fitness and determine if the disease is job-related.
The Company provides employees working in hazardous conditions with foods, milk, and other equivalent food products for therapeutic purposes in compliance with the applicable laws and corporate policies.
In addition, medical aid posts are in place to perform pre-shift and pre-trip check-ups and provide medical assistance to employees upon request.
Corporate Healthcare project
GRI 403–6
By 2025, Nornickel plans to provide its employees and their families with an easy and quick access to quality healthcare in line with the latest standards.
In 2022, the Company completed the first stage of the programme to upgrade its healthcare facilities and medical examination rooms for pre-trip and pre-shift check-ups. The first refurbished facilities with state-of-the-art equipment, medications, and expendables opened in Nornickel’s Polar Division. Primary care is provided by the Workshop Healthcare Service. General Practitioners (GPs) at Polar Division’s medical aid posts are responsible for helping those with urgent medical problems and delivering preventive health care to the Company’s employees. The service has started work to conduct staff health monitoring linked to job duties and analyse occupational disease factors and ways of mitigating them. The Company plans to open similar facilities at its other divisions in 2023.
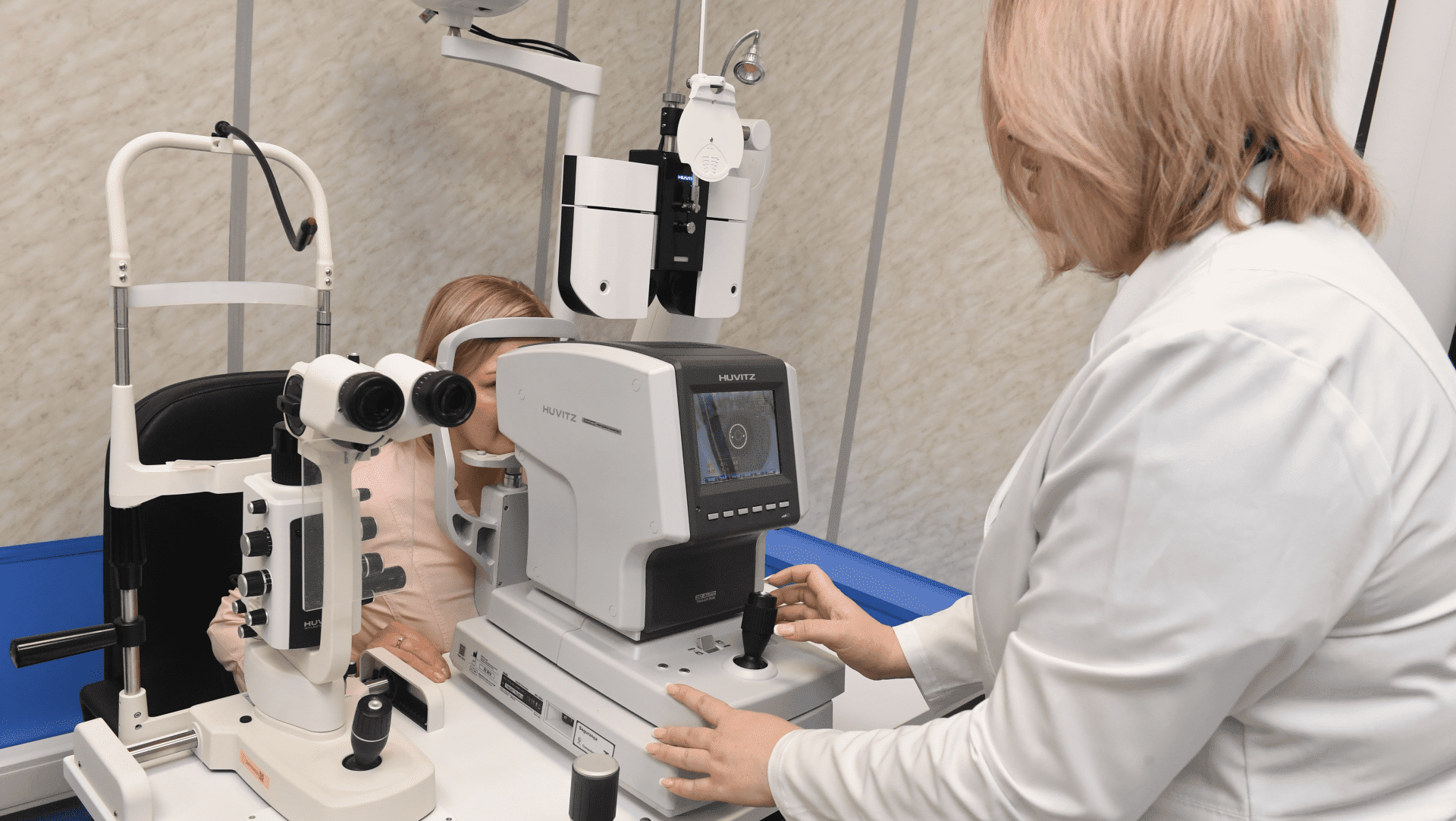
Nornickel’s corporate healthcare infrastructure
To provide our employees and their families with specialist medical services and highly qualified professionals, we are implementing a project to develop corporate healthcare across the Company’s footprint.
The Company is running projects to establish healthcare centres across its regions of operation to serve all local residents under the compulsory health insurance programme. In 2022, Nornickel completed repair and upgrade of new medical facilities – an MRI centre in Monchegorsk (serving local residents under the compulsory health insurance programme) and a corporate medical centre in Dudinka. The centres will open to their first patients in 2023.
Norilsk Division
In 2021, the Company opened its first corporate healthcare centre under the Z-Clinic brand in Norilsk, which has the most advanced equipment and highly professional medical staff. It provides medical help based on voluntary healthcare insurance (VHI) programme. Today, the centre offers a choice of 246 healthcare services in 12 primary care areas. Over the first year of its operation, it has delivered approximately 70,000 medical services. The waiting times for many specialists vary from seven days to one month, which confirms the high level of demand for healthcare services in the region.
Operating healthcare centre at Norilsk Division
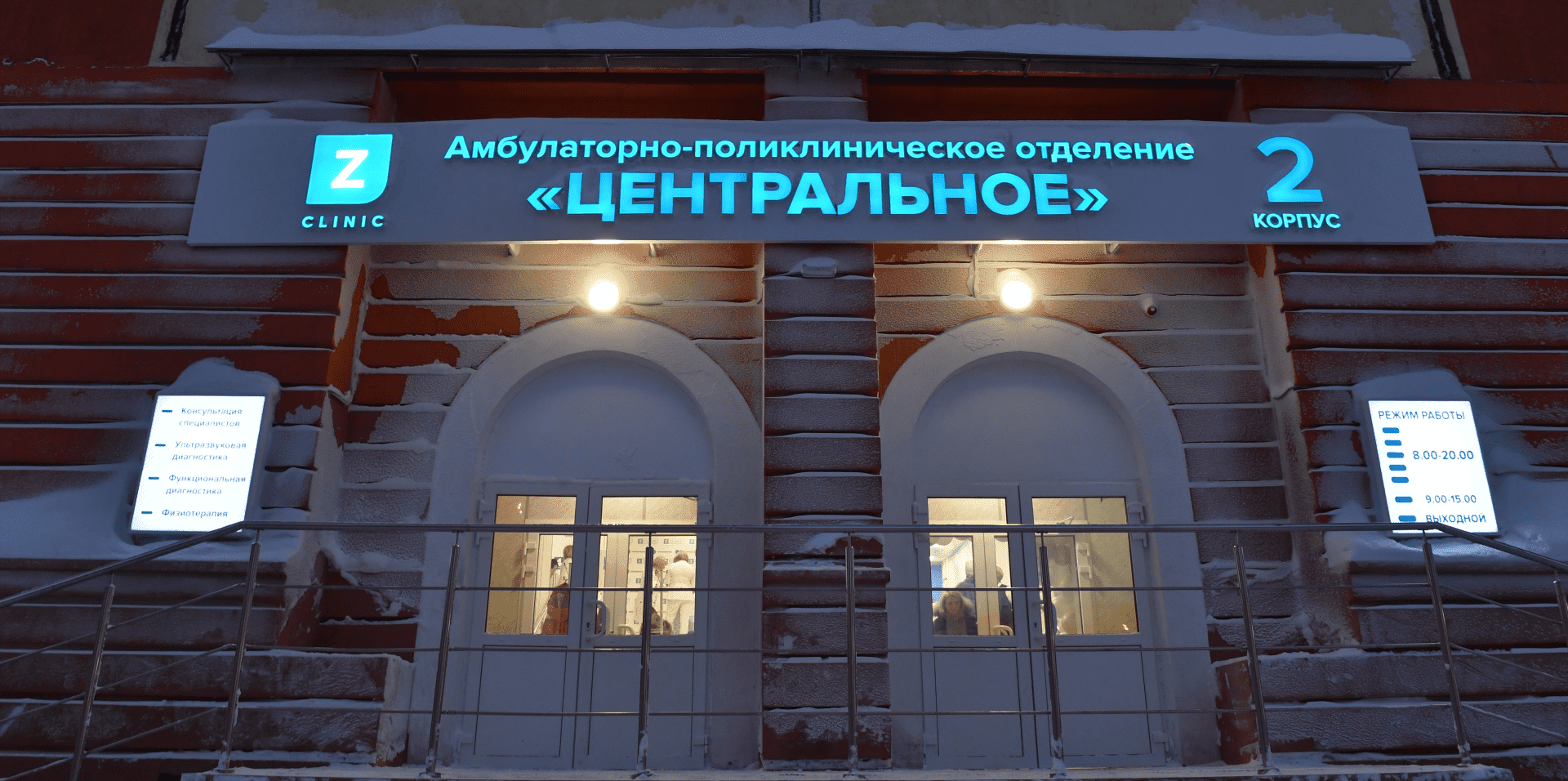
Healthcare centres at Norilsk Division – plans
In 2022, we continued to expand our network by including new centres to increase healthcare capacities in the region without replacing existing ones. The Company is getting ready to open two more corporate healthcare centres – in Norilsk’s Talnakh District and Monchegorsk. It also keeps on track its programme to develop small-scale healthcare departments in remote locations.
Kola Division
Healthcare centres at Kola Division – plans
Digital Medicine
Nornickel has an ecosystem of Digital Medicine services. Employees can use a mobile app for viewing their medical records, booking a medical appointment and finding all the necessary information about healthcare centres. The most popular services were added to the Nika corporate assistant and integrated into Nornickel’s superapp. The medical information system has been launched in 2022 in Norilsk and in 2021 in Zapolyarye Health Resort.
Mobile app and chatbot information system
Nornickel has also been active in promoting healthy lifestyle programmes. It is planning to launch several services to provide access to employees from all regions to relevant expert advice on healthy lifestyle and disease prevention.
Emergency preparedness
At Nornickel, we take a holistic approach to occupational health and safety, placing a strong emphasis on ensuring reliability of equipment and technological processes, preventing emergencies and addressing their impact on the environment and local communities.
To avoid occupational accidents, Nornickel implements risk-based occupational health and safety management.
In 2020, after the CHP-3 fuel spill, as part of the efforts to mitigate permafrost thawing risks and to prevent such emergencies in the future, NTEC launched the Buildings and Structures Monitoring System project designed to develop and deploy a comprehensive automated monitoring system for foundations and foundation soils in the Norilsk Industrial District. Capabilities under the first stage of the Projects have been successfully put into operation, with the automated monitoring systems covering 165 facilities (over 1,200 sensors deployed) and feeding data to the centralised IT platform. The Project’s objective is to ensure comprehensive automated monitoring for the safe operation of the Company’s assets, including for assessing the progress of permafrost thawing in the context of global climate change.
Nornickel’s facilities remain prepared for any emergencies, including emergency containment and response. This is vital as the Company operates more than 300 hazardous production facilities that rely on hazardous substances in their operational processes. Preparedness for emergencies is in line with Federal Law No. 116-FZ On Industrial Safety of Hazardous Production Facilities dated 21 July 1997.
The underlying document for emergency containment and response plans is the Regulations on Containment and Elimination of Accident Consequences at Hazardous Production Facilities approved by Resolution No. 1437 of the Russian Government dated 15 September 2020. They are approved by heads (deputy heads) of production units that operate such facilities, and heads (deputy heads responsible for approving action plans) of professional emergency rescue services and units engaged for emergency containment and response.
To ensure readiness for containment and elimination of accident consequences at hazardous production facilities, Polar Division signed contracts with a professional emergency rescue unit for mine rescue services and the maintenance of auxiliary rescue teams’ equipment. Auxiliary mine rescue teams were set up at Polar Division and Kola MMC hazardous production facilities (hazard classes 1 and 2) engaged in underground mining operations. Polar Division, Medvezhy Ruchey, Norilsk Production Support Complex, GRK Bystrinskoe, and Kola MMC hazardous facilities put in place surveillance, warning, communication, and support systems to rely on in case of emergencies. Mines are equipped with radio and positioning systems for employees, and telemetry system for underground machinery to track their locations. Hazard class 1 and 2 facilities operate local warning systems.
At the Group’s hazardous production facilities, drills are held regularly and the personnel is trained to deal with accidents, incidents, and emergencies.